Certification tracking is a task in which someone (or something) oversees employee certifications, tracking their validity and ensuring certifications are not expired at any point in time. Certification tracking is most common in industries that are certification-heavy. This means industries where a common workforce has a variety of qualifications, licenses, tickets, or certifications to be considered qualified workers.
Tracking certifications might seem like an easy task, but it involves a ton of organization to stay proactive when done manually. There are a variety of tools that allow companies to stay on top of certification tracking, automating their efforts and saving them time and money.
The most important thing to consider when tracking certifications is the expiry date. Employees performing day-to-day work with expired certifications are a ticking time bomb, ready to explode and significantly impact your company’s bottom line.
We will explore why you must always ensure staff has valid, up-to-date certifications and the costs that come with an unqualified workforce.
Table of Contents (Click to Jump to Each Section):
Expired Training: How Unqualified Workers Lead to More Injuries on the Job
Up-to-date training certifications play a very important role in the reduction of on-site injuries. When expiry dates are overlooked, workers are at a greater risk of being injured. The CDC reports that a lack of safety training contributes significantly to high injury rates. It is every employer’s responsibility to not only ensure that the proper training is present, but also confirming that the training is up to date.
Not to mention regulatory bodies like the Occupational Safety and Health Administration (OSHA) mandate that workers are legally required to be “qualified” to perform certain work safely. The definition of a qualified worker will differ by trade or job title, but let’s explore an example below for an electrician.
“Because of the potential for fatal accidents when electricity is concerned, OSHA defines qualified workers as those who have been fully trained to identify exposed live electrical parts and their voltage, and who have learned exactly what procedures to follow when they work on exposed live parts or are close enough to be at risk. Everybody else is “unqualified,” and you do not want any of them messing around with electrical wiring or trying to repair electrical equipment.”
In the above quote you will notice that OSHA mentions “fully trained.” This means the worker has ALL their required training, and that the training is invalid. Expired training DOES NOT qualify as valid training, and a worker carrying expired training certifications is not considered qualified.
In terms of compliance with regulatory bodies at the city, state, or federal (OSHA) level, many times you are legally bound to ensuring that none of your employee’s training has expired. If a training certification has expired, it is your responsibility to ensure that training is updated/renewed.
The Cost of Injuries on the Job
Alright, so what if you miss a training expiry and a worker gets injured? How bad can it be?
Injuries on the job impact your site in a variety of ways. An injury leads to lower morale, lower productivity, legal repercussions, worker’s compensation claims, time loss, all of which significantly impact your bottom line.
We have the numbers to show you why expired training is unacceptable. Let us explore the cost of injuries – keeping in mind that unqualified workers are far more likely to lead to injury-related costs.
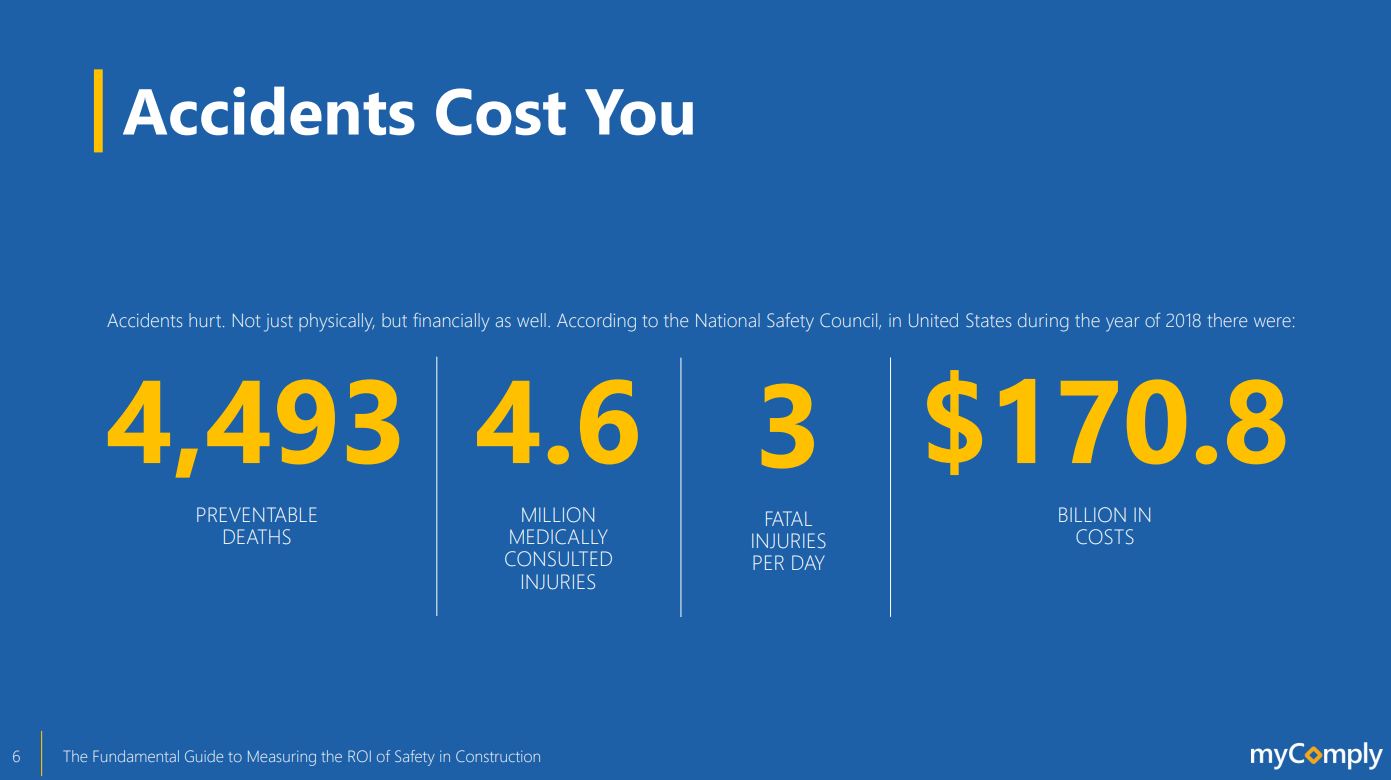
Know Exactly What an Accident or Injury Costs.
Contractors everywhere work hard to implement safety processes and procedures that promote safe work practice on the job. The goal is to avoid becoming a statistic noted in the picture above or one of the numbers listed below. A contractor must become intimately familiar with a quantifiable figure that represents the associated costs to a significant accident on-site. This number should be engrained in the project teams and should be one of the drivers to enforce safe practice.
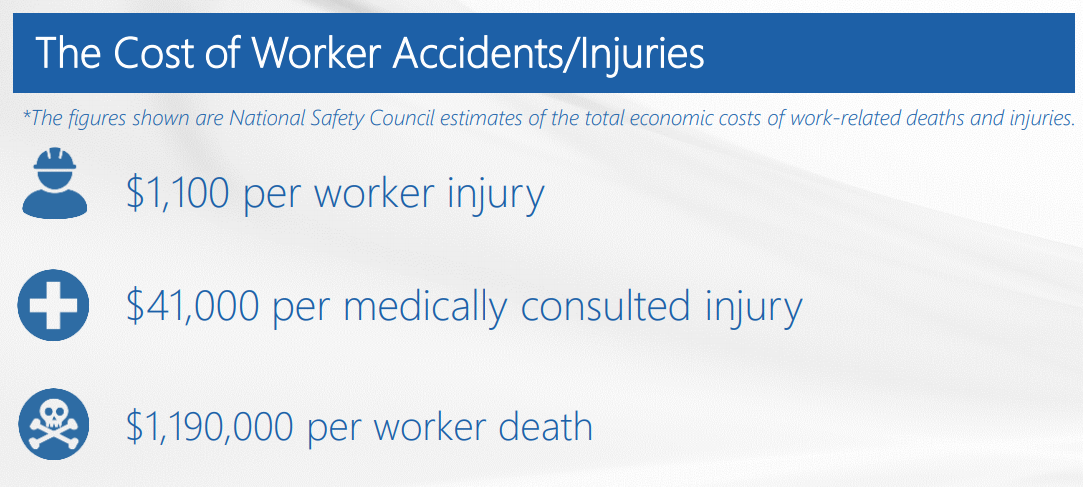
Understand Productivity Losses
Some costs are easily quantifiable, like medical costs, costs associated with insurance, and/or legal fees dealing with claims from a worker injury or death. What is not always easy to understand is the amount of money and time lost from a worker’s injury. The days that a worker is not on the job not only slows productivity on the job, but you are likely paying for that worker’s time away from the site. You may have to bring in new workers to fill the gap, which can all add up significantly.
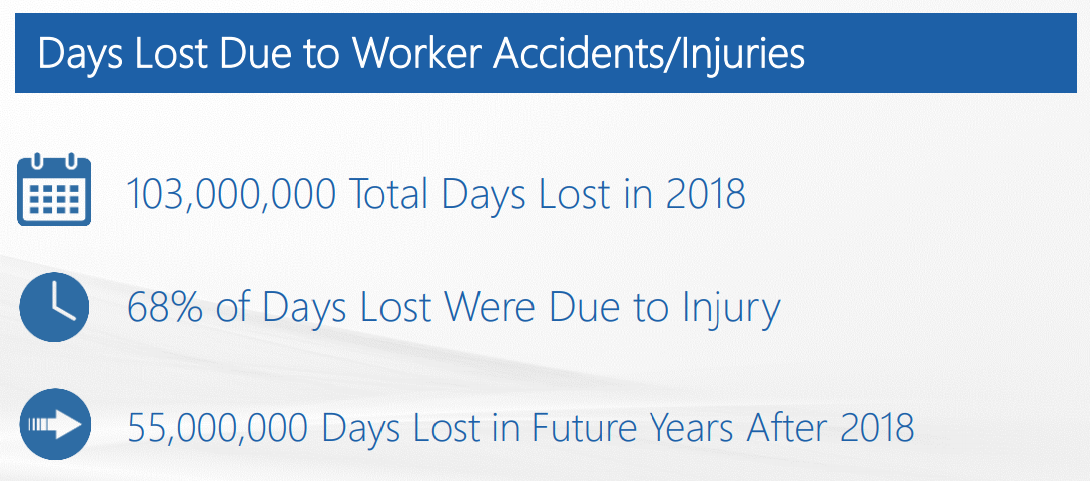
Hard Costs vs. Soft Costs
There are certain bills that pile up due to a workplace accident that are not always accounted for. Costs can be divided into two distinct categories: hard costs and soft costs.
• Hard costs are recorded easily on paper or by financial records. These costs can be calculated simply and clearly.
• Soft costs are the expenses that accrue after a workplace accident that is not directly recorded or billed on paper. These costs slow productivity, distract project teams and often go unrecorded leaving contractors unaware of the true cost of an accident on site.
Be aware of your hard costs first, and then ensure you explore the soft costs related to an accident. To calculate or understand your soft costs start by talking with every individual who was involved with the accident resolution. This can be admin staff, legal teams, project staff, etc.
We’ve listed some of the hard and soft costs but these costs certainly do not round the list:
Direct (Hard) Costs
• Wages
• Operational costs
• Insurance premiums and/or attorney’s fees
• Accidents and incidents
• Fines and/or penalties
Indirect (Soft) Costs
• Accident investigation
• Repairing damaged property
• Administrative expenses
• Worker stress in the aftermath of an incident resulting in lost productivity, low employee morale, and increased absenteeism
• Training and compensating replacement workers
• Poor reputation, which translates to difficulty attracting skilled workers and lost business share
Hard Cost Example: Dealing with Lawsuits, Litigation, and Legal Battles
In construction, the asset owner, general contractor, or permit holder holds some level of responsibility for every worker on their jobsite. In most other industries, this remains the same – the employer is liable for work performed under their supervision or on their property.
When it comes to workplace injuries, often there may be a dispute to see who is at fault or who is accountable for paying worker-related injury costs (worker’s compensation). As mentioned above, protecting the safety of your workforce starts with proper training. Likewise, protecting yourself against lawsuits and legal battles involves adequate training and verifying that the workforce is qualified to perform safe work.
Example) If a worker arrives on your jobsite with expired Fall Arrest Training, or no Fall Arrest Training at all and gets injured or dies from an accident while working at heights the first thing to be audited will be the worker’s qualifications.
Questions that are asked following any worker injury when determining who is liable:
• Did this worker have the proper training? Was it valid (not expired)?
• Were they supposed to be working at heights?
• Were they aware of the risks and properly trained to perform safe work?
If the company responsible for the worker is not able to confidently verify that they did everything in their power to ensure that the worker who was injured was prepared to perform safe work, then they will likely lose any legal battle related to the worker’s injury claim.
Certification tracking ensures that a company can confidently say, “We prepared all of the workers in our care to safely perform work on the job.” When a company is certain that their workforce is 100% qualified, they are far less likely to deal with crippling legal battles and liability associated to unsafe work.
Why is this a hard cost? Your legal fees have an invoice and most costs associated with a legal battle are directly quantifiable.
Soft Cost Example: Hurting Your Company Reputation
Your reputation matters. Whether it be winning new business or building relationships with external companies to move your company forward, your reputation as a company will play an enormous role in company success.
If your company has a track record for consistently ignoring worker safety by overlooking the importance of training certifications word will get around. Blue-collar industries are built on reputation and word-of-mouth; companies who place an emphasis on worker safety through certification tracking are the companies that win more business and attract more recruitment interest.
Nobody wants to work for a company that ignores their worker’s training, and likewise, nobody wants to award a bid to an organization that is known for mismanaging their worker’s training certifications.
Why is this a soft cost? Your reputation, ability to win competitive bids, and/or your attractiveness to job recruits are not directly quantifiable.
Your Reputation in Relation to Insurance Costs
Some may believe that a company’s reputation is just a matter of opinion, but in many blue-collar industries, a company’s track record is quantifiable. How? There are a variety of metrics that measure safety performance, a company’s risk level, and other indicators that a safety culture is emphasized.
One of the main calculations used by insurance firms is called Experience Modification Rating, or EMR. This is used widely in the construction industry and is used by insurance firms to price the cost of workers’ compensation premiums. The rating reflects a variety of lagging indicators, such as injury costs or claim history, and offers a prediction of future risk.
Your EMR Rating ties directly into your company’s ability to win competitive bids and implement a winning business development formula. Instead of shrugging your shoulders and wondering why you are not closing any new business, reflect on the reasons why your bids might be falling short. Many times, it comes down to risk and safety performance.
Companies that have certification tracking processes in place are far more likely to ensure a qualified workforce. Expired certifications and unqualified workers bring higher levels of risk, an increased likelihood of injury, and ultimately small (but frequent) accidents will compound over time impacting your business’s ability to win new business.
Safety is a profit-generating division, and expired certifications are unacceptable to companies looking to maintain or grow into world-class organizations.
Conclusion: Invest in Certification Tracking & Ensure Expiry Reminders
It is simple, more qualified workers = fewer injuries.
Qualified workers are workers with up-to-date training, workers with expired certifications present an enormous risk to employers.
So, how can we ensure your workforce is always qualified and that you NEVER miss an expiry date? Certification Management Software.
Certification Management Software makes certification tracking simple. The software automates a lot of manual work associated with tracking worker qualifications. Many organizations are still stuck using file folders, or they have adopted a digital strategy by using spreadsheet software to track certification expiry dates. While it is a step in the right direction it still poses the risk of human error or completely overlooking important expiry dates.
As mentioned earlier, employees who perform their jobs with expired tickets, training, and other certifications are ticking time bombs waiting to set off a fury of attacks on your bottom line. Don’t make the mistake of allowing workers with expired certifications to perform work, especially if you operate in a high-risk industry.
Certification tracking software is quite affordable and offers instant ROI when examining the various costs associated with worker injuries.
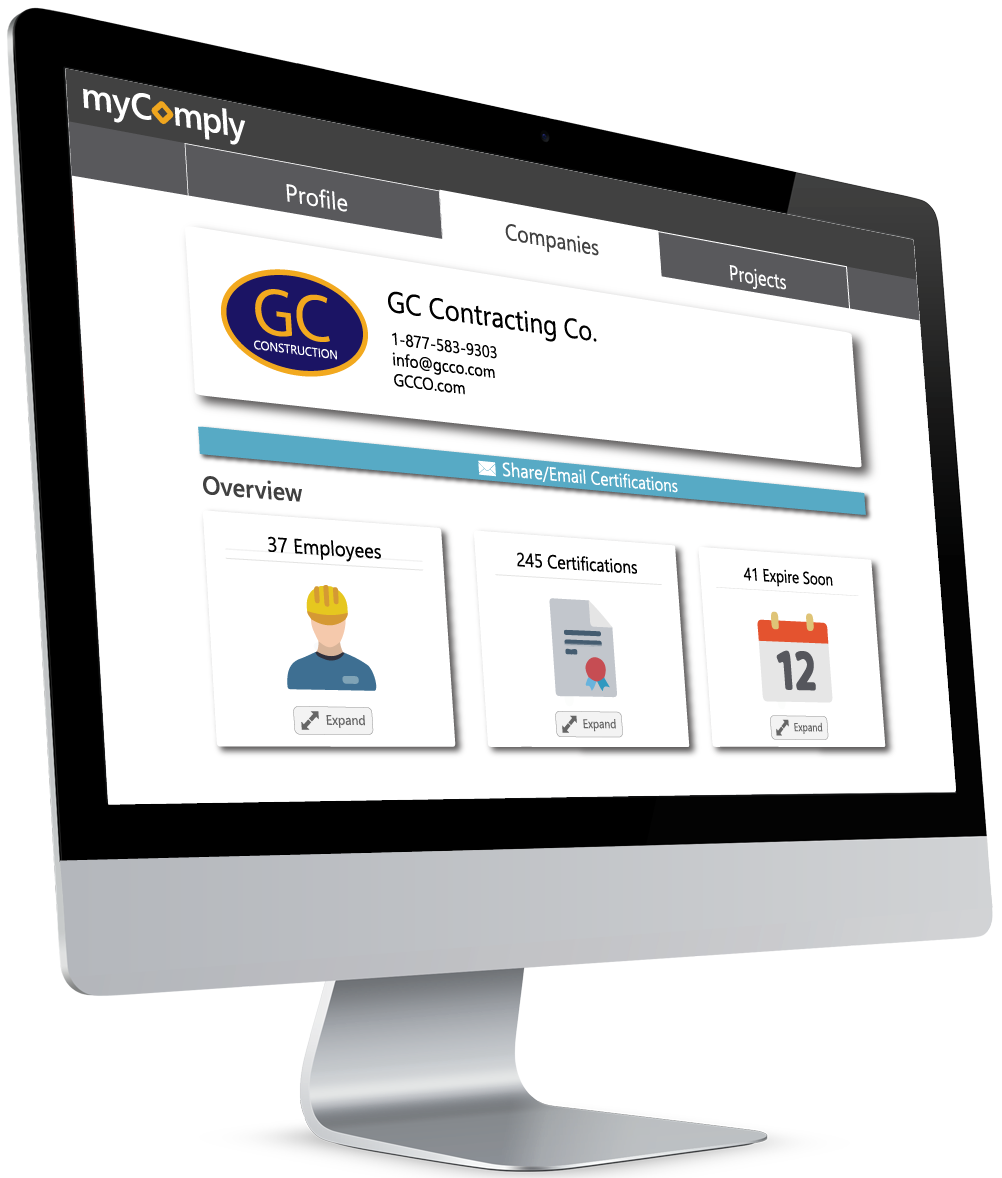
Learn how myComply’s Company Certification Management Software allows your company to manage workers and get detailed certification tracking for a low-cost. Click the button below for a short 15-minute demo of the software.